عملیات فورج – انواع فورج
در صنعت، فورج (Forge) به معنای کوره آهنگری، آهنگری کردن و کوبیدن است. عمل فورج نیز تکنیکی است که در آن فلزات با استفاده از نیروی فشاری متمرکز، به شکل و فرم مورد نظر تبدیل می شوند.
این روش یکی از مهمترین روش های فلزکاری در صنعت تولید مقاطع فلزی، به ویژه در صنایع آهن و فولاد است. نیروهای فشاری با استفاده از چکش یا پتک، پرس و غلتک بر قطعه فلزی وارد میشود.
برای انجام عملیات فورج، قطعه اولیه را که لقمه نامیده میشود در میان دو نیمه قالب قرار داده و نیروی بسیار زیادی به صورت آهسته و یا ضربه ای به آن اعمال میگردد.
با این شرایط قطعه گداخته شده درون قالب، شکل آن را به خود گرفته و مواد اضافی آن در حفره فلاش جمع میشوند. این مواد اضافی که دور ریز فورج نام دارند، در انتها از قطعه جدا میشوند.
مراحل اصلی عملیات فورج
عملیات فورج شامل چند مرحله اصلی است که هر کدام نقش مهمی در تولید قطعات با کیفیت دارند:
۱. انتخاب مواد اولیهاولین مرحله در فورج، انتخاب مواد اولیه مناسب است. فلزات مورد استفاده در فورج معمولاً شامل فولاد، آلومینیوم، تیتانیوم و آلیاژهای مختلف هستند. انتخاب مواد اولیه به نوع قطعه و کاربرد آن بستگی دارد. |
۲. گرم کردن فلزفلزات قبل از فورج باید تا دمای مشخصی گرم شوند. این دما بسته به نوع فلز و فرآیند فورج متفاوت است. گرم کردن فلز باعث نرمتر شدن آن و کاهش مقاومت در برابر تغییر شکل میشود. |
۳. تغییر شکل فلزپس از گرم شدن، فلز در قالبهای خاص قرار میگیرد و تحت فشار تغییر شکل میدهد. این فشار میتواند از طریق چکشهای هیدرولیک، پرسهای مکانیکی یا سایر دستگاههای فورج اعمال شود. |
۴. سرد کردن و پرداختپس از تغییر شکل، قطعات فورج شده باید به آرامی سرد شوند تا از ایجاد تنشهای داخلی جلوگیری شود. سپس قطعات ممکن است نیاز به پرداخت و ماشینکاری داشته باشند تا به شکل نهایی برسند |
انواع روشهای فورج – تفاوت فورج و ریخته گری
روش های آهنگری معمولا ضایعات کمی دارند یا بدون ضایعات هستند و می توانند هندسه قطعه نهایی را در مدت زمانی کوتاه در یک یا چند کورس فورج یا چکش ایجاد کنند. در تکنیک فورج عمل کوبیدن باعث شکلدهی فلزات بدون آسیب به جریان ذرات میشود و به همین دلیل فلز استحکام خود را حفظ میکند. در حال حاضر این فرایند، طبق درجه حرارت به این صورت طبقهبندی میشود:
· آهنگری سرد (Cold Forging )فورج سرد در دمای اتاق و در چند مرحله انجام میشود. دما در این نوع از آهنگری به حدی پایین است که فلز اکسید نشود به همین دلیل دقت ابعادی قطعات تولید شده با فورج سرد بسیار بالاتر از فورج گرم است. این روش برای فلزات نرمی چون آلومینیوم، سرب و… قابل اجرا است درحالی که فورج فولادها با این روش امکانپذیر نیست. |
فورج گرم تعادلی بین فورج سرد و داغ است، در این روش قطعه کار تا دمایی قبل از تبلور مجدد حرارت داده میشود. گرمای قطعه داغ به قالب و محیط منتقل میشود بدین ترتیب دمای خود قطعه کاهش مییابد. تنوع دمای فورج گرم حین انجام فرآیند موجب شده خواص ثابتی از ماده در دسترس نباشد. |
دمای آهنگری داغ بیشتر از دمای تبلور مجدد است. دمای بالا این فرآیند، تمایل به اکسید شدن را در قطعه افزایش میدهد، بنابراین نمیتوان دقت ابعادی دقیقی به دست آورد. |
| مقایسه انواع پالت فلزی و چوبی مزایا و معایب |
کاربردهای عملیات فورج
عملیات فورج در صنایع مختلف کاربردهای گستردهای دارد. برخی از مهمترین کاربردهای آن عبارتند از:
۱.فورج در صنعت خودروسازیدر صنعت خودروسازی، عملیات فورج برای تولید قطعاتی مانند میللنگ، چرخدندهها، سوپاپها و قطعات موتور استفاده میشود. این قطعات باید از استحکام و دوام بالایی برخوردار باشند. |
۲. فورج در صنعت هوافضادر صنعت هوافضا، قطعات فورج شده باید از وزن کم و استحکام بالایی برخوردار باشند. از این رو، از آلیاژهای سبک مانند تیتانیوم و آلومینیوم در این صنعت استفاده میشود. |
۳. فورج در صنعت نفت و گازدر صنعت نفت و گاز، فورج برای تولید قطعاتی مانند شیرآلات، اتصالات و لولهها استفاده میشود. این قطعات باید در شرایط سخت و دمای بالا مقاومت کنند. |
۴. فورج در صنعت ساختماندر صنعت ساختمان، فورج برای تولید قطعاتی مانند پیچ و مهره، اتصالات و سازههای فلزی استفاده میشود. این قطعات باید از مقاومت بالایی در برابر بارهای سنگین برخوردار باشند. |
۵. فورج در صنعت دفاعیدر صنعت دفاعی، عملیات فورج برای تولید قطعاتی مانند سلاحها، تجهیزات نظامی و قطعات خودروهای زرهپوش استفاده میشود. این قطعات باید از استحکام و دوام بالایی برخوردار باشند. |
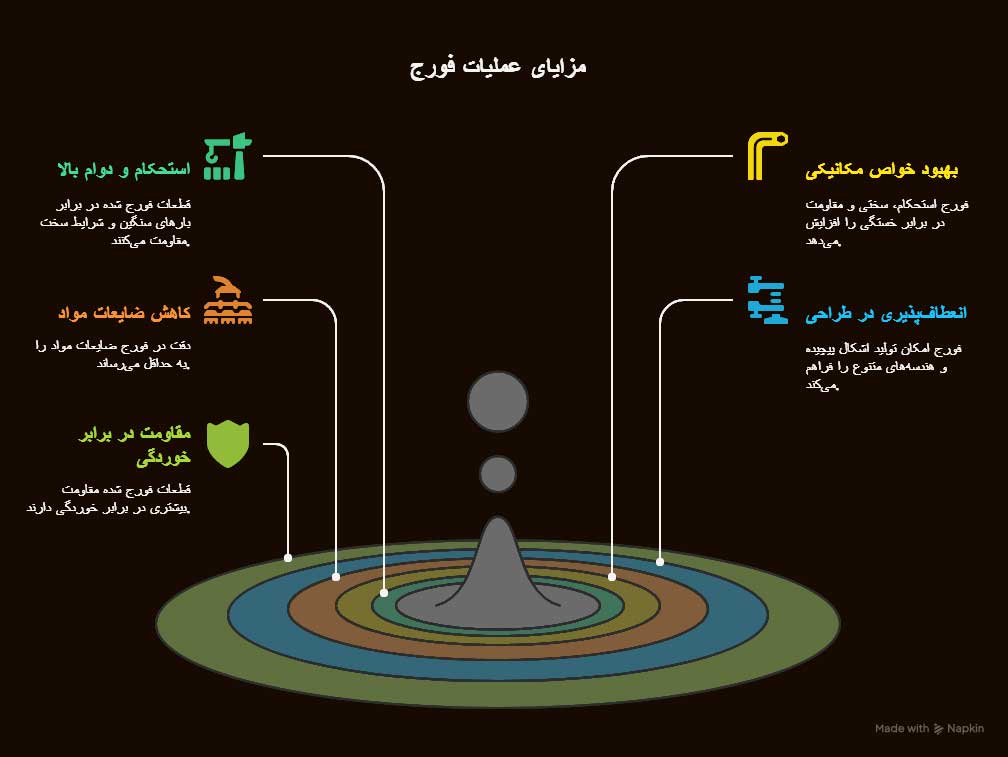
مزایای عملیات فورج
عملیات فورج به دلیل مزایای متعددی که دارد، در صنایع مختلف بسیار مورد استفاده قرار میگیرد. برخی از مهمترین مزایای آن عبارتند از:
۱. استحکام و دوام بالا
قطعات فورج شده به دلیل تغییر شکل در حالت جامد، از استحکام و دوام بالایی برخوردار هستند. این قطعات در برابر بارهای سنگین و شرایط سخت مقاومت میکنند.
۲. بهبود خواص مکانیکی
فورج باعث بهبود خواص مکانیکی فلزات مانند استحکام، سختی و مقاومت در برابر خستگی میشود. این ویژگیها باعث افزایش عمر مفید قطعات میشوند.
۳. کاهش ضایعات مواد
فورج به دلیل دقت بالا در تغییر شکل فلزات، ضایعات مواد را به حداقل میرساند. این ویژگی باعث کاهش هزینههای تولید میشود.
۴. انعطافپذیری در طراحی
فورج امکان تولید قطعات با اشکال پیچیده و هندسههای متنوع را فراهم میکند. این ویژگی باعث افزایش انعطافپذیری در طراحی قطعات میشود.
۵. مقاومت در برابر خوردگی
قطعات فورج شده به دلیل تراکم بالای مواد، مقاومت بیشتری در برابر خوردگی دارند. این ویژگی باعث افزایش عمر مفید قطعات در محیطهای خورنده میشود.
پیشنهاد مطالعه | انواع ریخته گری |
معایب عملیات فورج
با وجود مزایای متعدد، عملیات فورج معایبی نیز دارد که باید در نظر گرفته شود:
۱. هزینه بالای تجهیزات
فورج نیاز به تجهیزات پیشرفته و گرانقیمت دارد. این هزینهها ممکن است برای برخی شرکتها سنگین باشد.
۲. نیاز به نیروی متخصص
فورج نیاز به نیروی متخصص و آموزشدیده دارد. این موضوع میتواند هزینههای تولید را افزایش دهد.
۳. محدودیت در تولید قطعات بسیار بزرگ
فورج برای تولید قطعات بسیار بزرگ ممکن است با محدودیتهایی مواجه شود. این موضوع به دلیل محدودیت در اندازه قالبها و تجهیزات است.